PYMES
LOS ARANCELES Y EL CAMBIO CLIMÁTICO NO SALVARÁN LA INDUSTRIA MANUFACTURERA. LA IA INDUSTRIAL SÍ
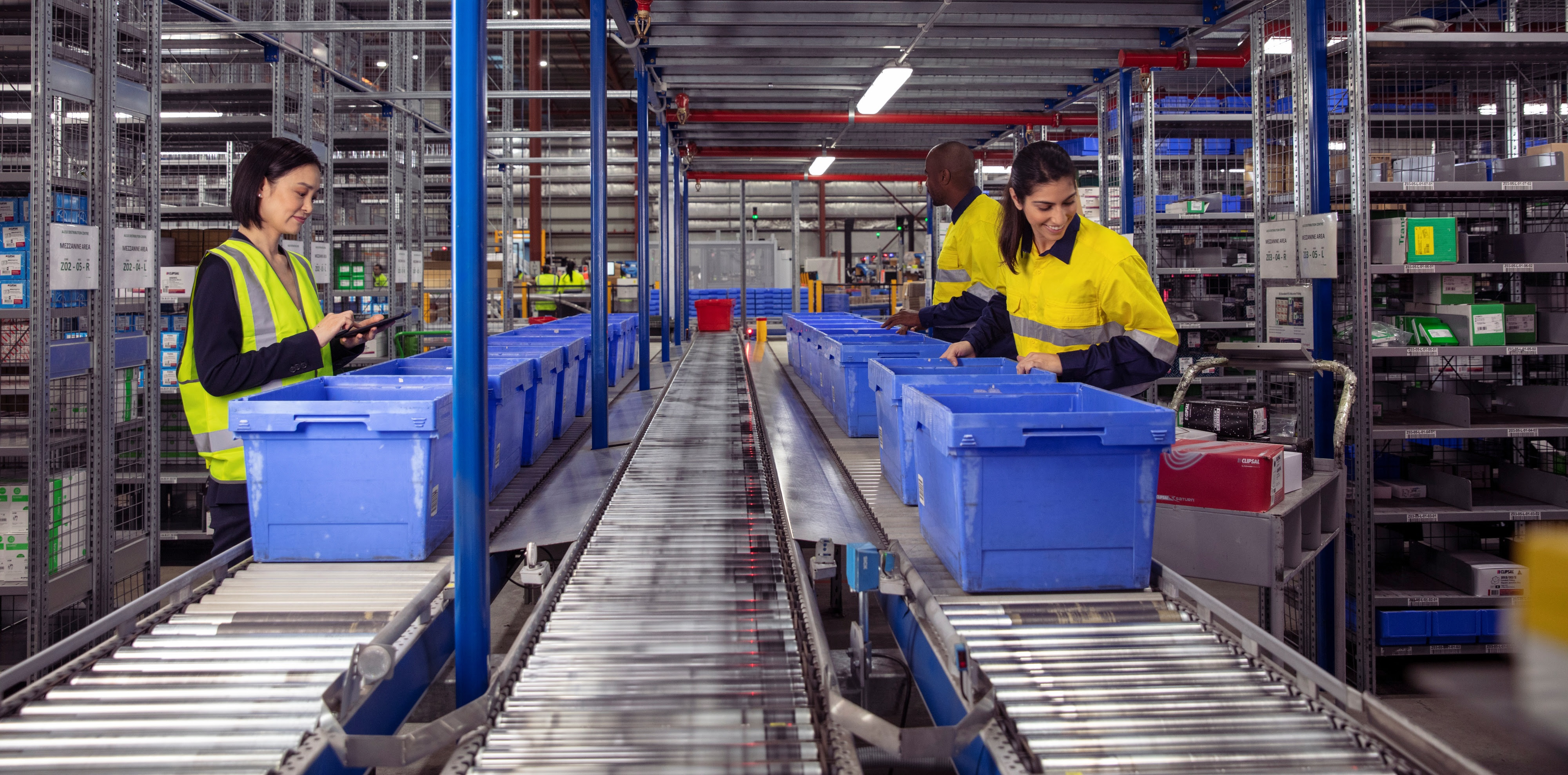
A medida que los fabricantes se enfrentan a las políticas de deslocalización y al impacto de los fenómenos meteorológicos extremos, las aplicaciones de IA industrial serán esenciales para mantener los costos, desbloquear la eficiencia de la producción y seguir siendo competitivos, dice Jim Chappell, director global de IA y análisis avanzado de AVEVA
Al visitar a un fabricante de automóviles en Dearborn, Michigan, el ejecutivo japonés Eiji Toyoda se llevó una sorprendente visión del inventario acumulado: ¿Qué pasaría si las piezas de automóviles se produjeran justo a tiempo para su uso? Esta brillante idea se adoptó por primera vez en Toyota Motor Corporation en la década de 1950, empresa que Toyoda llegó a dirigir. Tras la crisis del petróleo de 1973, el concepto se convirtió en un rasgo distintivo de la industria automovilística japonesa. Al minimizar el desperdicio y mejorar la calidad, el sistema de producción otorgó a los automóviles japoneses una reputación de fiabilidad y asequibilidad.
El ensamblaje justo a tiempo, a menudo llamado Lean Manuracturing, se ha convertido desde entonces en un pilar fundamental de la gestión global. Su adopción en las décadas de 1970 y 1980 se produjo en medio de períodos de estancamiento económico y alta inflación, mientras las empresas luchaban por mejorar los márgenes comerciales y recortar drásticamente los costos de producción, a la vez que producían más con menos. De 1973 a 1984, solo Toyota aumentó su producción de 170.046 unidades a 3,4 millones, según muestran los registros de la compañía. El resto del sector no tardó en seguir el mismo ejemplo.
Los riesgos nublan las previsiones para la industria manufacturera
Los fabricantes de todo el mundo se enfrentan hoy a un momento de transformación similar, aunque la situación mundial es muy distinta. Los problemas de la cadena de suministro relacionados con la COVID-19 pueden haberse aliviado en los últimos meses. Sin embargo, nuevos riesgos nublan las previsiones no solo a corto plazo, sino también para bien entrada la próxima década, como señaló el World Economic Form en su desalentador Informe de Riesgos Globales 2025. La turbulencia geopolítica y el surgimiento de un mundo multipolar están incrementando la demanda de producción local, mientras que los nuevos aranceles comerciales tendrán su propio impacto. Los fenómenos meteorológicos extremos, por su parte, seguirán pesando sobre el suministro de materias primas, incluyendo tanto insumos como recursos minerales.
Pero cuando las cosas se ponen difíciles, para replantear el viejo dicho, los duros recurren a nuevas herramientas. En cada crisis económica, la industria manufacturera ha aprovechado tecnologías y procesos de vanguardia para superar los obstáculos económicos y transformar los resultados empresariales. La tecnología de nuestros tiempos es la IA industrial, y el verdadero factor decisivo será su capacidad para generar información en tiempo real.
O ideas en el momento justo, parafraseando a Eiji Toyoda.
Liderando desde el frente con la transformación empresarial
Desde la adopción de la línea de montaje por parte de Henry Ford a principios del siglo XX hasta los sistemas Unimate de General Motors y Kanban y Justo a tiempo de Toyota, el sector manufacturero ha liderado la innovación y la transformación empresarial. La llegada de la Industria 4.0 ha acelerado la digitalización y ha impulsado el lanzamiento de plantas autónomas. Sin embargo, a medida que los fabricantes se enfrentan a disrupciones sin precedentes, la ventaja de ser pioneros en el contexto actual parece recaer en quienes adoptan el papel de los datos industriales y las tecnologías relacionadas con la inteligencia artificial (IA), como el aprendizaje automático, el análisis predictivo y la IA generativa.
Juntos, estos factores son fundamentales para proporcionar la información necesaria a fin de mantener las operaciones de fabricación optimizadas y eficientes. Cabe decir que la verdadera batalla no será entre las fábricas en el extranjero y las locales, sino entre las fábricas inteligentes y los modelos operativos obsoletos.
Esto es algo que los equipos de producción de Barry Callebaut han experimentado de primera mano. El fabricante suizo-belga comenzó a adoptar un enfoque digital para elaborar chocolate hace siete años, utilizando productos de software industrial avanzados para crear una fábrica inteligente que integra a las personas, los procesos y la tecnología. Al integrar la visualización empresarial con un sistema de ejecución de fabricación (MES) de última generación, el chocolatero mejoró la trazabilidad e impulsó la productividad. Con esta red digital conectada, ha eliminado los silos de datos y ha empoderado al personal información en tiempo real de toda la cadena de valor. Además, los modelos predictivos han revelado oportunidades de optimización para ajustes instantáneos, aumentando la capacidad de producción en un 10 %, mientras que la eficiencia en todo el sistema ha reducido el consumo de energía y ha encaminado al líder en productos de consumo hacia el logro de sus objetivos de cero emisiones netas sin sacrificar la producción.
Para mantenerse a la vanguardia de la industria chocolatera, Nestlé utilizó análisis avanzados con IA y datos en tiempo real en la nube para garantizar sabores consistentes en cada frasco de su bebida familiar Nesquik, a la vez que redujo el desperdicio de polvo en un 10 %. Con un ahorro de 101 g por frasco de 1 kg, se obtienen 10 tazas adicionales de Nesquik. La empresa ahora quiere expandir este éxito a más plantas y a otros productos como Ovaltine.
Mientras tanto, en Estados Unidos, New Belgium Brewing Co. ha pasado de ser una cervecería artesanal a ser líder nacional gracias a un enfoque digital, utilizando una plataforma MES junto con un software avanzado de control de operaciones. Gracias a una mejor programación operativa, visualización de procesos, análisis avanzado de IA, y una mejor colaboración e intercambio de conocimientos digitales, la empresa con sede en Colorado ha optimizado la producción, a la vez que ha mejorado la eficiencia y la calidad. En tan solo dos años, la eficiencia general de los equipos aumentó del 45 % al 65 %, mientras que el tiempo de inactividad se redujo un 50 %. Además, a pesar de las variables locales, las bebidas producidas en diferentes instalaciones de Estados Unidos ahora tienen el mismo sabor.
La mayoría de los fabricantes demandan nuevas tecnologías
A medida que más empresas buscan aprovechar estos avances transformadores, el 58% de los fabricantes afirma que la necesidad de nuevas tecnologías para empoderar a su fuerza laboral es un desafío empresarial fundamental, según el Informe de Inteligencia Industrial 2024 de AVEVA. De hecho, la gran mayoría (97%) cree que las soluciones de IA industrial y otras tecnologías digitales son más necesarias que nunca para seguir siendo competitivos en el desafiante panorama actual.
Sin embargo, la mayoría de los proyectos de transformación digital -el 78 % según un estudio de Capgemini- no logran los beneficios prometidos debido a una alineación deficiente con los resultados comerciales, una visibilidad limitada de las operaciones integrales y una información deficiente.
La respuesta reside en implementar sistemas flexibles y abiertos que integren a los equipos empresariales y operativos distribuidos en torno a un hilo de datos digital integral, donde puedan acceder a información empresarial en tiempo real a la escala que necesiten.
Al igual que el enfoque de producción de Eiji Toyoda, la información en tiempo real permitirá a los fabricantes afrontar condiciones operativas volátiles a medio plazo. Ante las políticas de deslocalización y las condiciones climáticas extremas, la capacidad del sector para mantenerse ágil y resiliente dependerá de cómo utilice los datos empresariales. La IA industrial es esencial para la fabricación del futuro.